山東埃爾派 | 點擊量:0次 | 2020-11-18
煤粉
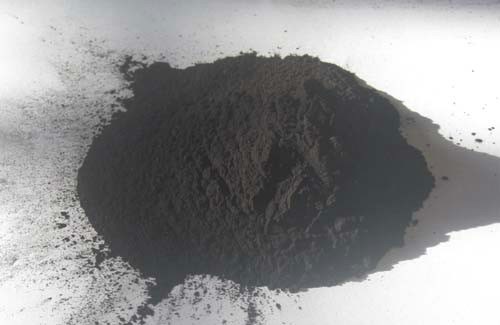
煤粉是指粒度小于0.5毫米的煤,是鑄鐵型砂中最常采用的附加物。近年來國外將煤粉類物質與粘土配成一種商品(碳粘土)供應市場。
鑄鐵用濕型砂中加入煤粉,可以防止鑄件表面粘砂缺陷,改善鑄件的表面光潔度,并能減少夾砂缺陷,改善型砂的潰散功能,對于濕型球鐵件,還能有效的防止產生皮下氣孔,可用圓形渦流燃燒器,空氣不用預熱。
物理特性
煤粉的主要物理特性有以下幾方面:
(1)顆粒特性煤粉是由尺寸不同、形狀不規則的顆粉所組成,一般煤粉顆粒直徑范圍為0-1000μm,大多20-50μm的顆粒;
?。?)煤粉的密度煤粉密度較小,新磨制的煤粉堆積密度過約為(0.45-0.5)t/m3,貯存一定時間后堆積密度為(0.8-0.9)t/m3;
?。?) 煤粉具有流動性煤粉顆粒很細,單位質量的煤粉具有較大的表面積,表面可吸附大量空氣,從而使其具有流動性。這一特性,使煤粉便于氣力輸送,缺點是易形成煤粉自流,設備不嚴密時容易漏粉。
均勻指數
細度值:煤粉細度值的大小,只說明煤粉中大于及小于x值的顆粒各多少,但并不能知道煤粉顆粒組成情況,即不知道其尺寸的均勻性如何。
均勻程度:表征煤粉顆粒均勻程度的指標,稱均勻性指數,也稱煤粉顆粒特性系數,用N表示。將煤粉分別用兩個不同篩號篩子篩分后。N值一般在0.8-1.3之間,N值越大,表明煤粉的均勻性越好。N值大小與磨煤機型式,粗粉離器型式等的關,比如,中速磨煤機比鋼球筒式磨煤機磨的煤粉均勻性要好,即其N值比較大。
理化特性:顆粒特性煤粉是由尺寸不同、形狀不規則的顆粉所組成,一般煤粉顆粒直徑范圍為0-1000μm,大多20-50μm的顆粒;煤粉為可燃物質,乙類火災危險品,粉塵具爆燃性,著火點在300℃~500℃之間,爆炸下限濃度34 g/m3~47g/m3(粉塵平均粒徑:5μm~10μm)。高溫表面堆積粉塵(5mm厚)的引燃溫度:225℃~285℃,云狀粉塵的引燃溫度580℃~610℃。
理化指標
揮發份:
煤粉在限定條件下隔絕空氣加熱后,揮發性有機物質的產率稱為揮發份,主要是由水份、碳氫的氧化物和碳氫化合物組成,但是煤粉中的物理吸附水和二氧化碳不屬揮發份之列。煤粉揮發份的高低是衡量煤粉質量好壞的主要指標之一,質量好的煤粉,揮發份含量較高,澆注鑄件時,在型腔內易形成還原性氣體,析出大量光亮碳,可以得到表面光潔的鑄件,但揮發份并非越高越好,揮發份含量超過40%,易。導致型砂發氣量增大,鑄件易產生氣孔,澆不足等缺陷,揮發份含量一般應控制在32-38%。煤粉在規定條件下完全燃燒后的殘留物,是煤礦物質在一定條件下經一系列分解,化合等復雜反應而形成的,是煤礦中礦物質的衍生物。
灰分:
含量的高低,直接反映出煤粉中殘留矸石含量的多少,如果煤粉灰分含量超過15%,導致煤粉補加量增大,長期使用,就會影響型砂的各項性能指標,一般應控制在10%以下或更低。
水份:
包括化合水和游離水,游離水在常壓下105度-110度的溫度下,經過短時間干燥即可全部蒸發,而化合水通常在200度-500度才能析出,因此在測定煤粉水份時,我們只是測定出游離水煤粉中的水份也是煤的雜質,在高爐噴吹煤粉中對水份要求比較嚴格,而在鑄造行業中煤粉中帶入的水份比例遠遠不及混砂時加入的水份,因此一般控制不太嚴格,應控制在6%以下,企業在選用煤粉時,不應該把水份指標作為衡量煤粉好壞的質量指標。
硫份:
通常分為有機硫和無機硫兩大類,煤粉中的硫主要以硫酸鹽硫,硫化鐵硫和有機硫三種形態存在。硫在煤粉中是一種極為有害的物質,控制的越低越好,硫份超過1.5%的煤粉,澆注時易生產大量的SO2和SO3物質,危害人體健康,顯著阻礙鑄件石墨化,易使鑄件形成白口傾向,因此一般應控制在1.0%以下或更低。
焦渣特征:
測定揮發份后坩堝中的殘留物,焦渣特征共分為8級,它反映煤粉在加熱干榴過程中軟化,熔融形成膠質體,膠質體的體積膨脹可部分堵塞砂型表面砂粒間的空隙,使鐵液不易滲入。但是,高結渣的煤粉容易以焦炭形勢與死粘土一起燒結在砂粒表面,形成多孔性薄殼,影響型砂其他性能。因此實際生產中各單位應根據自己的實際情況和使用效果,手工造型應控制在4-5級,高壓造型應控制在2-3級。
光亮碳:
煤粉在受熱時產生的碳氫揮發物在400度以上的高溫下裂解而在金屬和煤粉截面上析出一層帶有光澤的碳稱為光亮碳,其結構與石墨相似。近年許多鑄造專家深入隊煤粉的研究,以及對煤粉重視,對光亮碳這個引起了高度重視。光亮碳的析出量與材料與材料本身的揮發份有關,煤粉的光亮碳析出量一般應控制在8-13%,一般企業光亮碳含量控制在4-5%左右,就可獲得滿意的鑄件。
煤粉的制備
煤粉的制備是指通過磨煤機將原煤加工成粒度及水分含量均符合高爐噴煤要求的煤粉的工藝過程。高爐噴吹系統對煤粉的要求是:粒徑小于74μm的占80%以上,水分不大于1%。根據磨煤設備可分為球磨機制粉工藝和中速磨制粉工藝兩種。
球磨機制粉
球磨機制粉流程
中的原煤由給煤機2送入球磨機9內進行研磨。干燥氣經切斷閥14和調節閥15送入球磨機,干燥氣溫度通過冷風調節閥13調節混入的冷風量來實現,干燥氣的用量通過調節閥15進行調節。
干燥氣和煤粉混合物中的木屑及其他大塊雜物被木屑分離器10捕捉后由人工清理。煤粉隨干燥氣垂直上升,經粗粉分離器11分離,分離后不合格的粗粉返回球磨機再次碾磨,合格的細粉再經一級旋風分離器4和二級旋風分離器5進行氣粉分離,分離出來的煤粉經鎖氣器12落人煤粉倉8中,尾氣經袋式收粉器6過濾后由二次風機排人大氣。
一次風機出口至球磨機人口之間的連接管稱為返風管。設置此管的目的是利用干燥氣余熱提高球磨機人口溫度和在風速不變的情況下減輕袋式收粉器的負荷,但生產實踐證明此目的并沒有達到。
此流程要求一次風機前常壓運行,一次風機后負壓運行,在實際生產中很難控制,因此,在20世紀90年代初很多廠家對上述工藝流程進行了改造,改造后的工藝流程如圖7-2b所示。改造的主要內容有:
(1)取消一次風機,使整個系統負壓運行;
(2)取消返風管,減少煤粉爆炸點;
(3)取消二級旋風分離器或完全取消旋風分離器。改造后大大簡化了工藝流程,減小了系統阻力損失,減少了設備故障點。
中速磨制粉
中速磨制粉工藝流程
煤倉中的原煤經給煤機送入中速磨中進行碾磨,干燥氣用于干燥中速磨內的原煤,冷風用于調節干燥氣的溫度。中速磨煤機本身帶有粗粉分離器,從中速磨出來的氣粉混合物直接進入袋式收粉器,被捕捉的煤粉落人煤粉倉,尾氣經排粉風機排人大氣。中速磨不能磨碎的粗硬煤粒從主機下部的清渣孔排出。
按磨制的煤種可分為煙煤制粉工藝、無煙煤制粉工藝和煙煤與無煙煤混合制粉工藝,三種工藝流程基本相同?;诜辣?,煙煤制粉工藝和煙煤與無煙煤混合制粉工藝增加以下幾個系統:
(1)氮氣系統:用于惰化系統氣氛。
(2)熱風爐煙道廢氣引入系統:將熱風爐煙道廢氣作為干燥氣,以降低氣氛中含氧量。
(3)系統內O2、CO含量的監測系統:當系統內O2含量及CO含量超過某一范圍時報警并采取相應措施。煙煤和無煙煤混合制粉工藝增加配煤設施,以調節煙煤和無煙煤的混合比例。
上一篇: 滑石粉
下一篇: 玄武巖